TECHNOLOGICAL INNOVATION
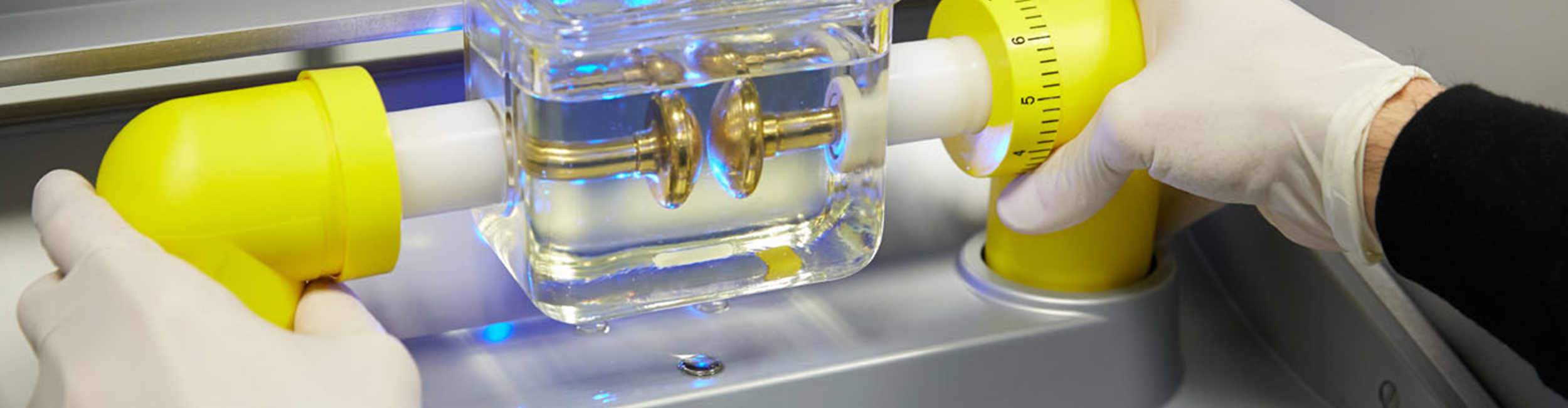
Objective of the Project
The main objective of the Innovation Group is to create a collaborative technology strategy between partner organizations and companies, so that the territory becomes a reference in the field of precision technologies.
Objective of the Project
Three lines of technology work linked to precision technologies.
Important steps and dates
First Team of Technology Center and Training Centers: Armeria Eskola, Ideko, IMH Campus and Tekniker.
Addressed to:
Aimed at companies that need advice on a technological and/or research challenge.
Results obtained
- First team of technology and training centres.
- Meetings and sessions have been highly appreciated..
- 3 lines of work involving 8 companies.
- A new project launched.
4 areas of knowledge
Development of precision mechatronic systems (design, simulation and assembly)
- 1 -
In this vector we can find projects carried out between centres of knowledge related to precision technologies: means of production, means of measurement and means of manipulation.
Zero-fault manufacturing processes
- 2 -
Technology allows us increasingly advanced and accurate manufacturing. In this vector we can find projects related to precision technologies, from advanced manufacturing to the connectivity and exploitation of technology in industry 4.0.
Precision methodology and engineering laboratories and infrastructure
- 3 -
Knowledge agents have the necessary tools and infrastructure to carry out metrology and precision engineering projects..
Digitalization
- 4 -
This vector includes media digitization, development of simulation tools and models, connectivity to the digital media platform, AI algorithm, and Blockchain technology.
Metrology and precision engineering
laboratories and infrastructure
These are the laboratories and infrastructure available to companies in the district:
- Simulation and optimization of system behavior: structural, thermoelastic, fluidodynamic. Modeling behavior and integrating compensation to improve accuracy based on different calibration modes.
- IIoT system digitized manufacturing machine park..
- Machining and metrology workshop with predefined technologies.
- Demostradores 4.0
- The metrology lab, a large ultraviolet room and a assembly workshop, where these systems are usually manufactured and assembled..
Examples of projects
Development of a measurement tool to characterize the diameters of the Cassette Body (CB) Multilink hinge component for ITER
Tekniker, in collaboration with F4E, has developed a high-precision mechatronic system for measuring the internal diameter of components" for the scientific project Divertor Cassette Body (CB) Multilink hinge ITER. It is a portable measuring instrument with a measurement uncertainty of more than 4 µm for measuring the internal diameters of these large components.
Multilateration integrated in machine tools
The integration of the multilateration principle on a MH allows to optimize and reduce the time and measurement uncertainty of the traditional volumetric verification process of a MH. The integration of a length measurement system on the machine has the advantage of performing a periodic control of the geometrical health of the MH to ensure its optimal condition throughout the life cycle of the production environment.
Calibration of industrial robots with laser tracker technology
Tekniker, in collaboration with RoboDK, has launched a technology service for calibrating industrial robots. The process of characterization and compensation of the absolute accuracy of robotsynstrials can be defined in several stages: verification, calibration and validation. Specific cinematic parameters are used through RoboDK software to program routes. This allows the generation of corrected programs based on DH parameters and real rigidity parameters obtained in the calibration process. The results show that the accuracy of an order of magnitude can be improved.
Control of the manufacturing process of machining and assembly lines
In order to ensure stable and accurate production processes, both in machining and assembly, work is done on the monitoring and digitization of all key parameters that will enable the achievement of simple control and monitoring indicators. Combining this digitization of the plant with process knowledge allows rapid decision-making, reducing deficiencies and improving the productivity and final accuracy of the product. Client: LUCCHINI (Italy).
Examples of projects
Development of a measurement tool to characterize the diameters of the Cassette Body (CB) Multilink hinge component for ITER
Tekniker, in collaboration with F4E, has developed a high-precision mechatronic system for measuring the internal diameter of components" for the scientific project Divertor Cassette Body (CB) Multilink hinge ITER. It is a portable measuring instrument with a measurement uncertainty of more than 4 µm for measuring the internal diameters of these large components.
Multilateration integrated in machine tools
The integration of the multilateration principle on a MH allows to optimize and reduce the time and measurement uncertainty of the traditional volumetric verification process of a MH. The integration of a length measurement system on the machine has the advantage of performing a periodic control of the geometrical health of the MH to ensure its optimal condition throughout the life cycle of the production environment.
Calibration of industrial robots with laser tracker technology
Tekniker, in collaboration with RoboDK, has launched a technology service for calibrating industrial robots. The process of characterization and compensation of the absolute accuracy of robotsynstrials can be defined in several stages: verification, calibration and validation. Specific cinematic parameters are used through RoboDK software to program routes. This allows the generation of corrected programs based on DH parameters and real rigidity parameters obtained in the calibration process. The results show that the accuracy of an order of magnitude can be improved.
Control of the manufacturing process of machining and assembly lines
In order to ensure stable and accurate production processes, both in machining and assembly, work is done on the monitoring and digitization of all key parameters that will enable the achievement of simple control and monitoring indicators. Combining this digitization of the plant with process knowledge allows rapid decision-making, reducing deficiencies and improving the productivity and final accuracy of the product. Client: LUCCHINI (Italy).